What is oil casing pipe?
Oil casing pipe is a key pipe used in oil and gas drilling projects to reinforce the wellbore of oil and gas wells, isolate the formation, and protect the integrity of the wellbore. It constitutes the main body of the well structure and directly affects the safety, production efficiency and life of oil and gas wells.
Each well uses several layers of casing according to different drilling depths and geological conditions. After the casing is lowered into the well, cement is used for cementing. Unlike oil pipes and drill pipes, it cannot be reused and is a one-time consumable material. Therefore, the consumption of casing accounts for more than 70% of all oil well pipes.
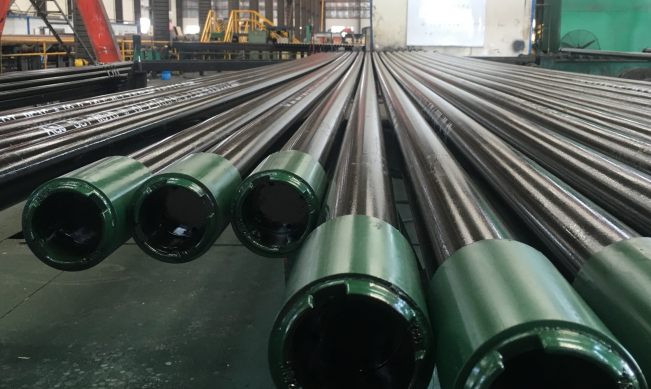
The main functions of casing pipe:
1. Well support: prevent wellbore collapse and maintain wellbore stability;
2. Formation isolation: separate formations with different pressures or fluid properties (such as water layers and gas layers);
3. Fluid channel: provide production channels for oil and gas to prevent pollution;
4. Anti-corrosion protection: reduce the erosion of downhole acidic media (H₂S, CO₂) on the pipe string;
5. Completion foundation: provide installation foundation for subsequent completion tools (such as packers and Christmas trees).
Types of drilling casing:
In the process of oil production, casing can be divided into: conductor, surface casing, intermediate casing and production casing according to its use.
1. Conductor: used for initial support of shallow well sections.
2. Surface casing: protect drilling to avoid pollution from shallow water and shallow gas layers, support wellhead equipment and maintain the weight of other layers of casing.
3. Technical casing: used to isolate temporary support under complex geological conditions such as high-pressure layers and salt-gypsum layers. Separate the pressure of different layers so that the drilling fluid can circulate normally and protect the production casing. Install anti-burst devices, leak-proof devices and tail pipes in the well.
4. Production casing: After drilling is completed, it is retained in the wellbore for a long time as the core channel for oil and gas production, protecting the wellbore from erosion by formation fluids and providing installation space for downhole tools. Direct contact with the production layer fluid requires high pressure resistance and corrosion resistance.
Casing steel grade and standard:
Oil casing is the lifeline to maintain the operation of oil wells. Due to different geological conditions, the stress state downhole is complex, and the combined effects of tension, compression, bending and torsion stress act on the pipe body, which puts higher requirements on the quality of the casing itself. Once the casing itself is damaged for some reason, it may lead to a reduction in production of the entire well or even scrapping.
According to the strength of the steel itself, OCTG casing can be divided into different steel grades, namely H40, J55, K55, N80, L80, C90, T95, P110, Q125, V150, etc. Different well conditions and well depths require different steel grades. In corrosive environments, the casing itself is also required to have corrosion resistance. In places with complex geological conditions, the casing is also required to have anti-collapse performance. The casing steel grade follows international standards such as API 5CT, and some imported products comply with ASTM standards.
Steel Grade
|
Yield Strength (MPa)
|
Features
|
Typical Applications
|
H40
|
276-552
|
Low cost, low strength
|
Shallow well casing
|
J55/K55
|
379-552
|
Economical, general
|
Shallow wells, water wells
|
N80
|
552-758
|
Medium to high strength, balanced cost performance
|
Medium to deep well technical casing
|
L80
|
552-758
|
Contains Cr (13%), corrosion resistant
|
Wells containing CO₂/H₂S
|
C90/T95
|
621-862
|
Anti-sulfur stress corrosion
|
High sulfur gas fields
|
P110
|
758-965
|
Ultra-high strength
|
Deep wells, shale gas fracturing sections
|
Q125
|
862-1034
|
Dedicated for ultra-deep wells
|
Ultra-deep wells, high temperature and high pressure wells
|
Special steel grades:
13Cr/Super 13Cr: CO₂ corrosion resistance (used in acidic gas fields)
Duplex steel (22Cr/25Cr): Cl⁻ corrosion resistance (deep sea, high salt environment)
Nickel-based alloy (Alloy 825): H₂S+CO₂+high temperature resistance (extreme working conditions)
Characteristics of oil casing pipe:
(1) Structural characteristics
Seamless steel pipe (mainstream) or straight seam ERW welded pipe (used in some shallow wells)
Threaded connection: API standard thread or special thread type, such as VAM, FOX.
Multi-layer casing combination: conduit → surface casing → technical casing → production casing
(2) Performance characteristics
1. High strength: excellent tensile, extrusion and internal pressure resistance, such as N80 and P110 steel grades.
2. Corrosion resistance: Some steel grades contain alloys such as Cr and Mo, which are resistant to H₂S/CO₂ corrosion (such as L80-13Cr).
3. Sealing: Special threads ensure high-pressure gas sealing.
4. Adaptability: It can cope with extreme working conditions such as high temperature (≤350℃) and high pressure (100+MPa).
Oil casing pipe specifications:
When oil casing is produced, the outer diameter is usually 114.3 mm to 508 mm.
The wall thickness is adjusted according to the strength and well conditions, usually between 6.45 mm and 16.1 mm.
There are three casing lengths specified by API:
R-1: 4.88 meters to 7.62 meters;
R-2: 7.62 meters to 10.36 meters;
R-3: 10.36 meters and above.
(1) The casing length is not fixed, ranging from 8-13m. However, casings not shorter than 6m can be provided, and their quantity shall not exceed 20%.
(2) There shall be no folds, hairlines, delamination, cracks, rolling and scarring on the inner and outer surfaces of the casing. These defects shall be completely removed, and the removal depth shall not exceed 12.5% of the nominal wall thickness.
(3) There shall be no defects such as folds, hairlines, delamination, cracks, rolling and scarring on the outer surface of the coupling.
(4) The threaded surface of the casing and coupling shall be smooth, and burrs, tears and other defects that are sufficient to interrupt the thread and affect the strength and tight connection are not allowed.
Manufacturing process:
Seamless Casing: no welds, strong pressure bearing capacity, high cost. Suitable for high-pressure wells and deep wells.
Straight seam welded pipe (ERW Casing): high production efficiency and low cost, but the welds need to be strictly tested. Suitable for shallow wells and low-pressure wells.
Application areas of OCTG casing pipe:
Classification by well type:
1. Shallow well (<3000m): You can choose J55/K55 steel grade, common specifications are: 9-5/8", 7".
2. Medium-deep well (3000-5000m): You can choose N80/P110 steel grade, common specifications are: 7", 5-1/2".
3. Deep well/ultra-deep well (>5000m): Q125/V150 steel grade can be selected, common specifications are: 5-1/2", 4-1/2"
4. Shale gas horizontal well: P110+special buckle steel grade can be selected, common specifications are: thick wall 5-1/2".
Special environment application:
High sulfur gas field: L80, C90 sulfur-resistant steel grade
Deep-sea oil field drilling: duplex steel + anti-corrosion coating
Geothermal well: 13Cr high temperature resistant casing
What is OCTG pipe?
OCTG (Oil Country Tubular Goods, oil special pipe) is a general term for special pipes used for drilling, completion and oil production in the oil and gas industry, mainly including:
Casing Pipe: reinforcement of well wall, isolation of formation.
API Tubing: oil and gas production channel.
Drill pipe: transmit drilling pressure and torque.
Core functions:
1. Ensure the structural integrity of the wellbore
2. Prevent formation fluid from channeling
3. Adapt to high temperature, high pressure, and corrosive environments
Anti-corrosion measures for oil casing pipe:
1. First of all, ensure that the water quality meets the standards and strictly test and manage the water quality. Implement separate injection of sewage and clean water, strengthen the cleaning of the main water pipeline, ensure that the water quality in the station and at the bottom of the well meets the standards, and reduce the introduction of corrosion sources into the annular space;
2. For newly commissioned water injection wells, adopt annular space protection fluid mainly for sterilization, and form a system for regular injection;
3. In view of the accelerated effect of mechanical abrasion on the corrosion of oil casing, it is recommended to add a rubber ring to the oil pipe coupling or a centralizer to the part with severe well deviation to avoid corrosion during the operation process and water injection. During the process, the oil pipe scratches the casing and one side contacts the casing;
4. In view of the serious bacterial corrosion under the scale and the slow growth and killing of SRB at high temperature, 100 degrees Celsius high-temperature water or water vapor can be regularly injected into the annulus to kill the SRB under the scale;
5. Before the corrosion in the casing of the water injection well is effectively controlled, it is not recommended to promote the use of cathodic protection and coated casing.
Conclusion:
Oil casing is the "skeleton" of oil and gas wells. Its steel grade, size and material need to be comprehensively selected according to the well depth, pressure, corrosion environment, etc. From low-cost J55 to super-strong Q125, different steel grades meet diverse needs, while special materials (such as 13Cr, duplex steel) cope with extreme working conditions. In the future, high-performance, intelligent and environmentally friendly casing will become the direction of technological development.